Background
Although plants can recover from critical levels of xylem embolism, < 50% loss of hydraulic conductivity in conifers (Brodribb and Cochard, 2009) and < 88% in angiosperms (Urli et al., 2013), the exact mechanism is still under debate. The ascent of sap is driven by the evaporative demand from the atmosphere, which generates a negative pressure (i.e., tension) in the water column and hydrogen bonds between molecules (i.e., cohesion) pull the sap through the plant via the well accepted cohesion-tension theory (Dixon, 1896; Angeles et al., 2004). However, positive xylem sap pressure can be recorded under particular conditions, for example water-saturated soil combined with very low transpiration. This mechanism has been shown to refill embolized vessels in springtime (Sperry et al., 1994) and in species that experienced freeze-thaw induced embolism (Charrier et al., 2013 and 2014). Refilling of embolized vessels has been hypothesized to occur under both positive and negative xylem sap pressures in Laurus sp or Vitis sp, for example (Salleo et al., 1996). However, the ‘refilling under tension’ mechanism is inconsistent with the cohesion-tension theory (Zwieniecki and Holbrook, 2000). Moreover, recent works suggest that refilling occurs only under positive pressure in Vitis (Charrier et al., 2016). The dynamic changes in xylem sap pressure therefore need to be explored at both the seasonal and diurnal scale while maintaining as much as possible the integrity of the hydraulic architecture of the plant.
Although the use of stem psychrometers has been extensively described since the 80’s (e.g., Dixon and Tyree, 1984; Tyree and Dixon, 1986), the measurement of positive xylem sap pressure is relatively rare. The protocol described here allows the quantification of the spatio-temporal pattern of bulk xylem sap water potential under positive pressures, and even moderate tensions (maximum of 0.05 MPa) along the water column using non-invasive sensors (i.e., point pressure sensors).
Materials and Reagents
- Parafilm M (Bemis, catalog number: PM996 )
- Stainless-steel hypodermic needle 21 G 1 ½” (Terumo Medical, catalog number: 8AN2138R1 )
- Union–1/16” PEEK (Interchim, catalog number: 869290 )
- Lock ring (Ark-Plas Products, catalog number: LEX66-PP0 )
- Threaded male Luer connector 10-32 UNF (Ark-Plas Products, catalog number: LGX74-PP0 )
- Reinforced PVC flexible tubes (RS Components, catalog number: 440-874 )
- Zip ties e.g., RS Pro Black Nylon Non-Releasable Cable Tie, 300 x 4.8 mm (RS Components, catalog number: 233-487 )
- 4-way Luer Lock Stopcock, Male-Male-Female (Cole-Parmer, catalog number: EW-30600-04 )
- Stainless steel high quality single edge blades (e.g., Mure & Peyrot, catalog number: 144.3 )
- Nylon Hose clips (RS Components, catalog number: 291-587 )
- Cutting disk (RS Components, catalog number: 448-7439 )
- HSS Drill bit, 0.8 mm diameter (e.g., RS Components, catalog number: 457-651 )
Note: Most parts are available from the laboratory equipment suppliers.
Equipment
- High resolution datalogger (e.g., Campbell Scientific, model: CR1000 )
- Pressure transducer 30Psi (Honeywell International, catalog number: 26PCDFA6D )
- Stabilized power supply 12V DC (e.g., Traco Power, catalog number: TML 20212C )
- Hand-held driller
Procedure
Directly attaching a pressure sensor at the distal end of a cut stem (i.e., pressure gauge) allows quantitative measurement of the pressure however at the cost of removing the upper part of the plant. Another approach, less interfering but still invasive (i.e., point pressure sensor), is to connect the pressure sensor to the xylem via a stainless steel hypodermic needle (Clearwater et al., 2007; Thitithanakul, 2012, see Figure 1). The latter allows plant functions (e.g., transpiration) to continue and pressure to be recorded at different heights along the water column. Xylem sap pressure is measured by a pressure transducer connected to a datalogger that records the output signal (positive or negative). The connection between the sensor and the xylem has to be perfectly sealed using Parafilm in order to accurately estimate the pressure.
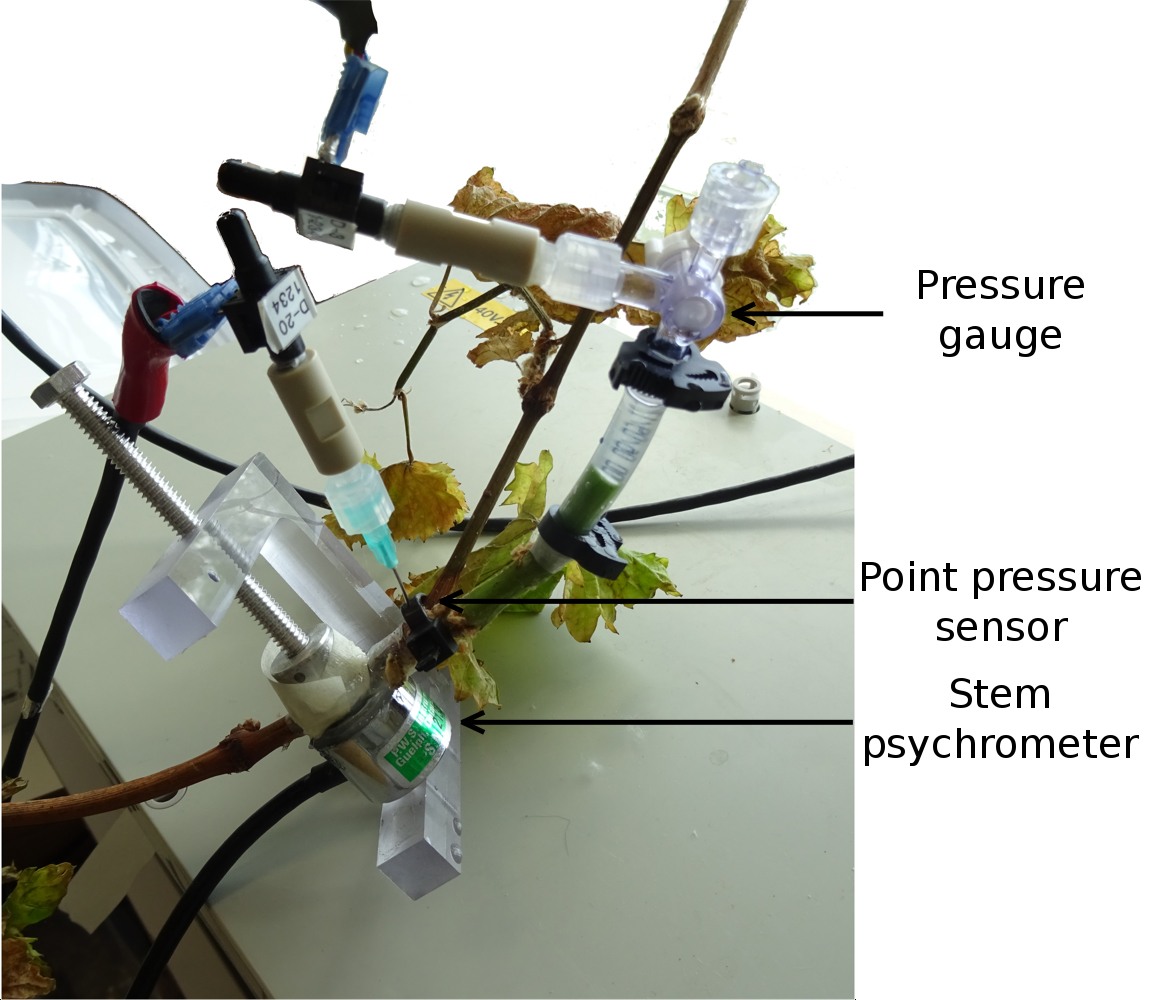
Figure 1. Distal part of a grapevine plant (Vitis vinifera cv. Grenache) showing examples of the three distinct instruments. From bottom to top, stem psychrometer PSY-1, point pressure sensor and pressure gauge.
- Preparation of the sensor (Figure 2)
Wrap the threaded end (10-32 UNF) of the pressure transducer (#1 Figure 2) and the male Luer connector (#3 Figure 2) with Parafilm and screw up at both ends of the union 1/16” piece (#2 Figure 2). Place the Luer lock (#4 Figure 2) onto the male Luer connector. Fill the sensor with deionized degassed water to remove all air bubbles.
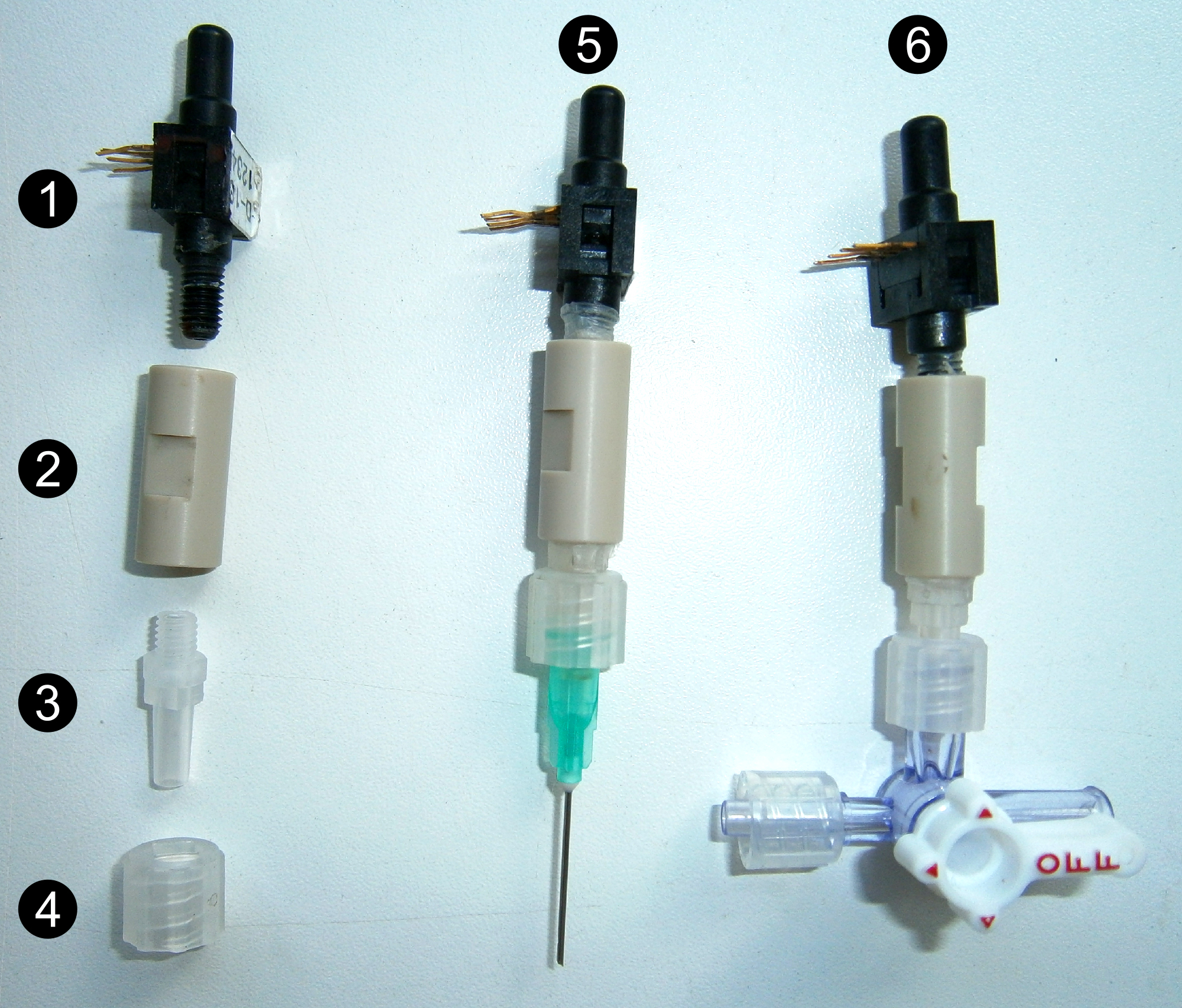
Figure 2. Different parts and assembly of the sensors. Pressure transducer (1), union 1/16” piece (2), male Luer connector (3) and Luer lock (4), point pressure sensor (5) and pressure gauge (6).
- Pressure gauge (#6 Figure 2)
Connect a 3 cm-long piece of adapter tubing to the 4-way Stopcock. Wrap the region of interest of the distal end of the stem with Parafilm, cut the stem 2-3 times under water with a sharp blade. Remove bark and cambium over 1 cm using the blade and immediately insert the cut end into the adapter tubing, tighten with a collar. Fill the whole system up with deionized and degassed water to remove all air bubbles using a syringe.
- Point pressure sensor (#5 Figures 2 and 3)
- Using a small disk, gently make a notch 2.0 cm from the base of the stainless steel hypodermic needle (21 G 1 ½”; #1-2 Figure 4), and cut the needles at 2.1 cm. Remove all barbs and make sure that the needle is not plugged using a needle of smaller diameter . Drill a hole of the exact diameter of the needle 1 cm away from the lock of the zip tie. Insert the needle into the hole and wrap the basal 2.0 cm with Parafilm (#3 Figure 4).
- Drill a hole of the exact diameter of the needle in the stem using a drill bit (0.8 mm diameter for 21 G 1 ½” needles). Pierce to the xylem and then wash it with deionized water. Gently insert the stainless steel hypodermic needle, previously filled with water, into the hole. The notch of the needle must locate within the xylem (Figure 3). Tightly fix the needle with the zip tie.
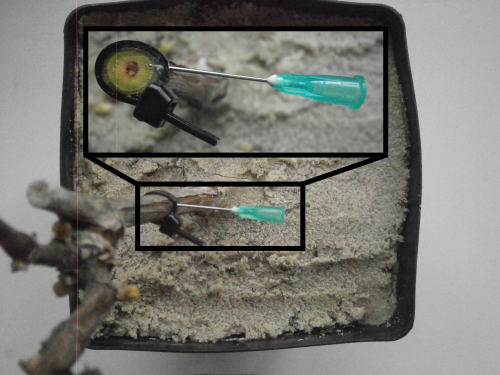
Figure 3. Point pressure sensor inserted into a grapevine plant. The frame illustrates the cross-section of the stem and shows the insertion of the needle into the stem xylem.
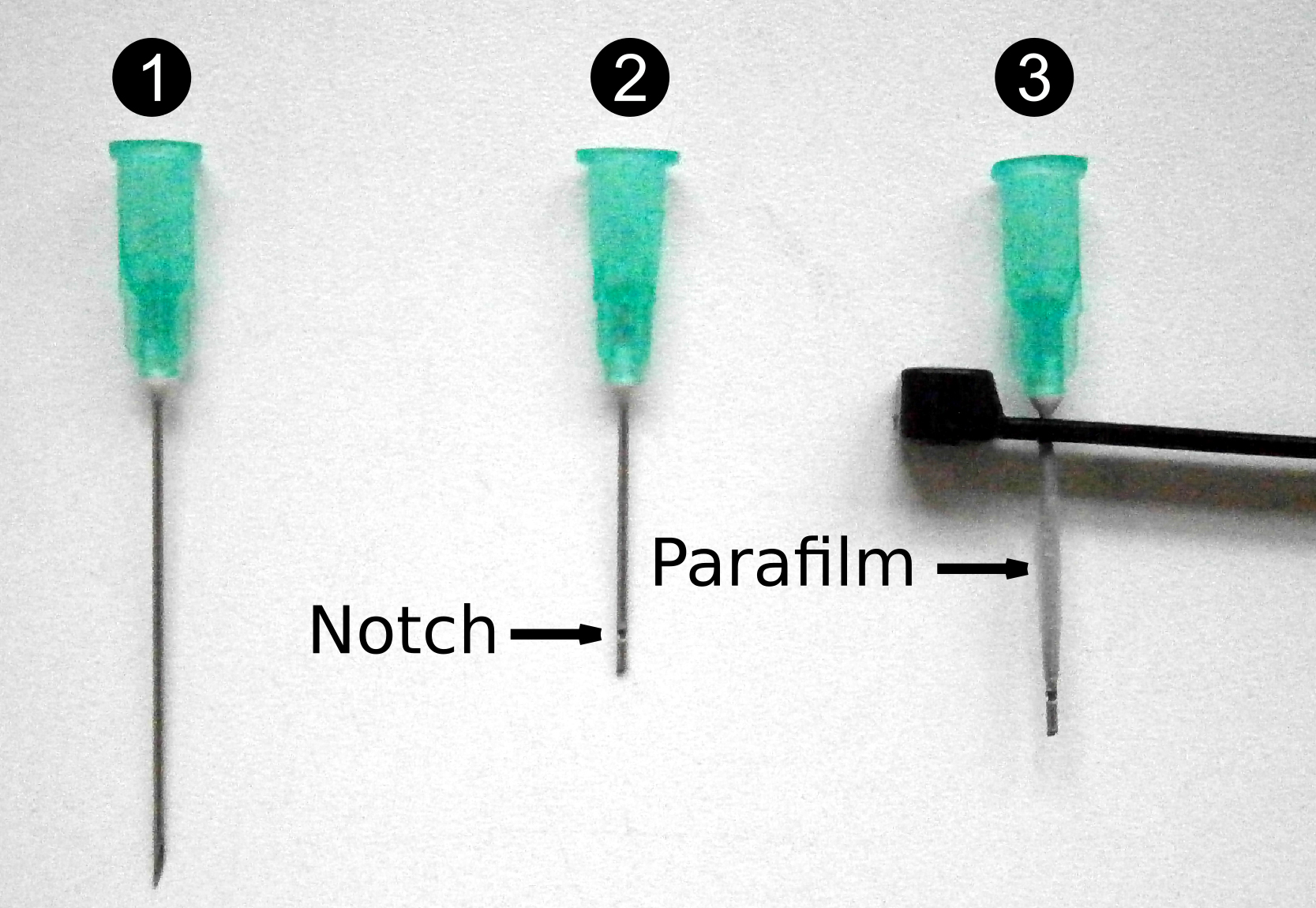
Figure 5. Connection of the point pressure sensor. Once the inserted needle is filled with deionized and degassed water (1), the sensor is screwed onto the needle (2, 3).
- Connection of the sensor (Figure 5)
Fill both pressure sensor and inserted needle with deionized degassed water (#1 Figure 5), and screw them together (#2 Figure 5). Connect the pressure transducer to the datalogger, with stabilized 10 or 12 V (D.C) input voltage.
Data analysis
- Each pressure transducer has a slight offset from atmospheric pressure. It is therefore recommended to measure the output signal (the offset U0) for a short period of time (e.g., > 5-10 measurements by the datalogger) before any measurement (calibration or connecting the pressure transducer to the xylem of a plant).
- Calibration can be performed using a pressure gauge to measure the output signal along the normal operating range of the sensor (e.g., 30 Psi [ca. 0.2 MPa] for 26PCFFA6D sensors; Figure 6). The output tension (Uout) depends on the input tension (Uin) and the calibration coefficient of the sensor. It therefore should be normalized if Uin is not stable along the experiment (e.g., battery supply over a long period).
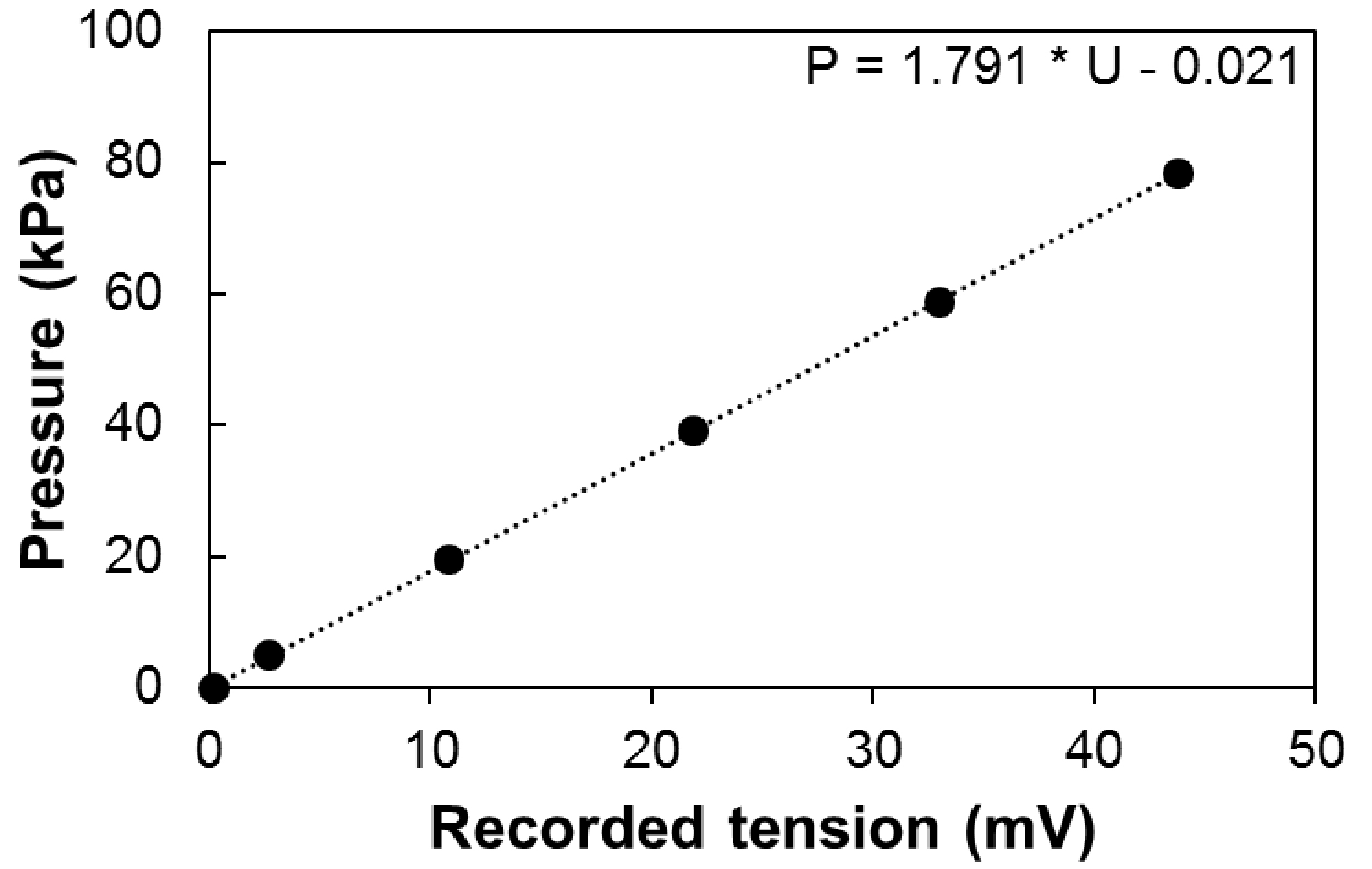
Figure 6. Calibration of the sensor. Pressure depending on the recorded tension Uout, with constant input tension (Uin = 12V).
- The pressure is therefore equal to:
P = α·k·(Uout - U0)
where, P is the pressure in kPa, Uout is the output signal in mV, U0 is the offset in mV, k the calibration coefficient of the sensor in kPa mV-1 and α, the ratio between Ucal (the input tension during calibration) and Uin.
- Correcting the effect of temperature on the output signal.
Uout is affected by the temperature resulting in 3.5 kPa variation in apparent pressure over the 10-20 °C range in both a closed sensor (orange line Figure 7) and a sensor connected to an excised plant i.e., detached from the root system (green line Figure 7).
The change in apparent pressure depending on the temperature is used to correct the apparent pressure (Figure 8): sensor connected to the excised plant (U0 = 0.530·θ - 9.60) or closed sensor (U0 = 0.482·θ - 11.12).
However, the discrepancy between apparent and corrected pressure is relatively small compared to the pressure generated by the plant (50 kPa or more in intact plant, vs. ca. 3.5 kPa in control sensors, in this example).
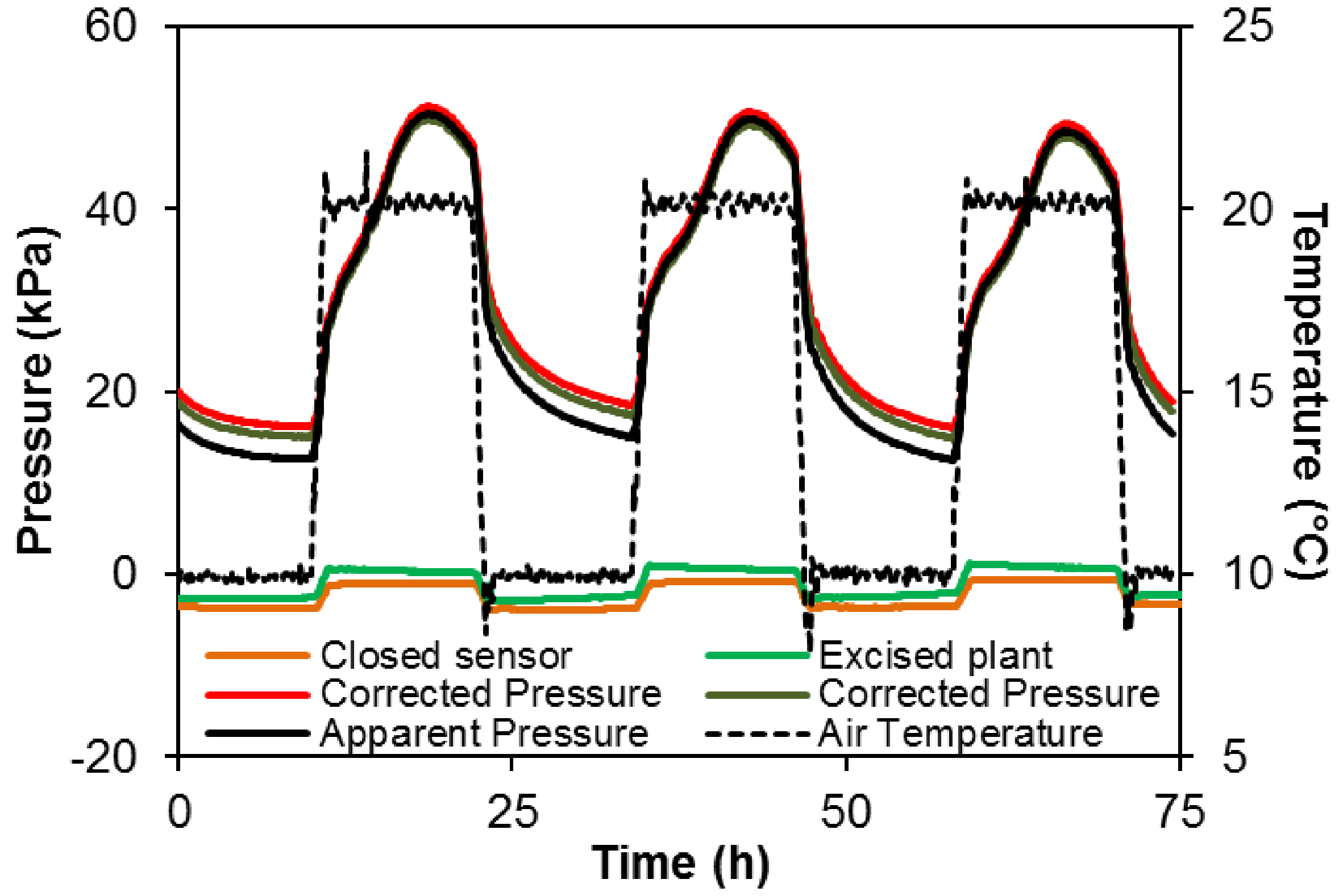
Figure 7. Variation in temperature (+ 20/10 °C; dotted black line) and the effect on the recorded signal from a pressure sensor alone (orange line) or inserted in a cut grapevine plant (without root system, green line). The change in the apparent pressure (ca. 0.35 kPa °C-1) has to be taken into account in data analysis. The solid black line represents the apparent pressure recorded in an intact grapevine and red and brown lines the corrected pressure according to the correction using sensor alone or inserted in a cut plant, respectively.
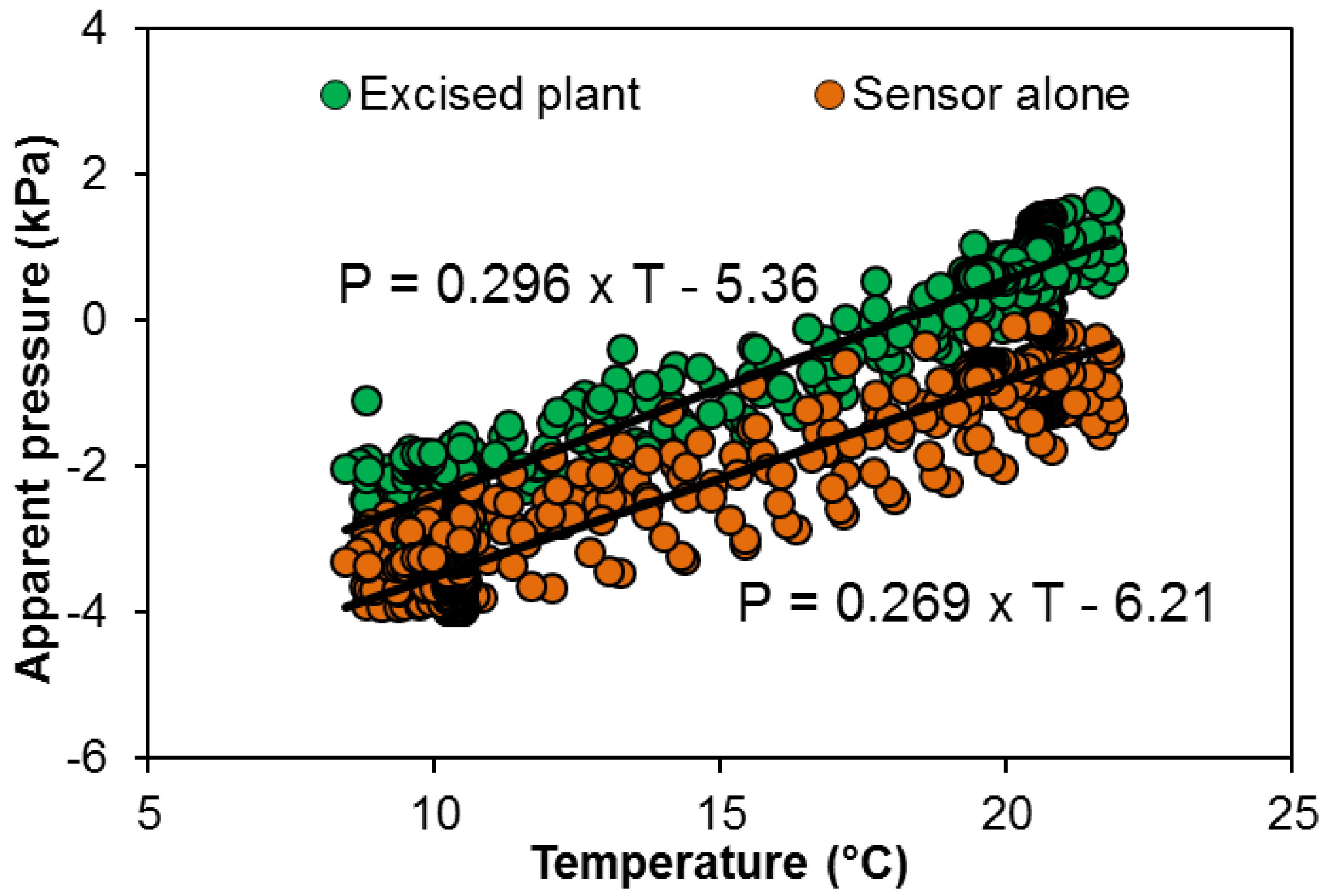
Figure 8. Apparent pressure depending on air temperature in a closed pressure sensor (orange dots) or inserted in a cut grapevine plant (without root system, green dots)
Acknowledgments
This study has been carried out with financial support from the Cluster of Excellence COTE (ANR-10-LABX-45, within Water Stress project), and AgreenSkills Fellowship program, which has received funding from the EU’s Seventh Framework Program under grant agreement FP7 No. 26719 (AgreenSkills contract 688).
References
- Angeles, G., Bond, B., Boyer, J. S., Brodribb, T., Brooks, J. R., Burns, M. J., Cavender-Bares, J., Clearwater, M., Cochard, H., Comstock, J., Davis, S. D., Domec, J., Donovan, L., Ewers, F., Gartner, B., Hacke, U., Hinckley, T., Holbrook, N. M., Jones, H. J., Kavanagh, K., Law, B., López-Portillo, J., Lovisolo, C., Martin, T., Martínez-Vilalta, J., Mayr, S., Meinzer, F. C., Melcher, P., Mencuccini, M., Mulkey, S., Nardini, A., Neufeld, H. S., Passioura, J., Pockman, W. T., Pratt, R. B., Rambal, S., Richter, H., Sack, L., Salleo, S., Schubert, A., Schulte, P., Sparks, J. P., Sperry, J., Teskey, R. and Tyree, M. (2004). The cohesion-tension theory. New Phytologist 163(3): 451-452.
- Brodribb, T. J. and Cochard, H. (2009). Hydraulic failure defines the recovery and point of death in water-stressed conifers. Plant Physiol 149(1): 575-584.
- Charrier, G., Charra-Vaskou, K., Kasuga, J., Cochard, H., Mayr, S. and Ameglio, T. (2014). Freeze-thaw stress: effects of temperature on hydraulic conductivity and ultrasonic activity in ten woody angiosperms. Plant Physiol 164(2): 992-998.
- Charrier, G., Cochard, H. and Ameglio, T. (2013). Evaluation of the impact of frost resistances on potential altitudinal limit of trees. Tree Physiol 33(9): 891-902.
- Charrier, G., Torres-Ruiz, J. M., Badel, E., Burlett, R., Choat, B., Cochard, H., Delmas, C. E., Domec, J. C., Jansen, S., King, A., Lenoir, N., Martin-StPaul, N., Gambetta, G. A. and Delzon, S. (2016). Evidence for hydraulic vulnerability segmentation and lack of xylem refilling under tension. Plant Physiol 172(3): 1657-1668.
- Clearwater, M. J., Blattmann, P., Luo, Z. and Lowe, R. G. (2007). Control of scion vigour by kiwifruit rootstocks is correlated with spring root pressure phenology. J Exp Bot 58(7): 1741-1751.
- Dixon, H. H. (1896). On the osmotic pressure in the cells of leaves. Proceedings of the Royal Irish Academy (1889-1901) 4: 61-73.
- Dixon, M. A. and Tyree, M. T. (1984). A new stem hygrometer, corrected for temperature gradients and calibrated against the pressure bomb. Plant Cell Environ 7(9): 693-697.
- Salleo, S., Gullo M. A. L., Paoli, D. and Zippo, M. (1996). Xylem recovery from cavitation-induced embolism in young plants of Laurus nobilis: a possible mechanism. New Phytologist 132: 47-56.
- Sperry, J. S., Nichols, K. L., Sullivan, J. E. and Eastlack, S. E. (1994). Xylem embolism in ring-porous, diffuse-porous, and coniferous trees of northern Utah and interior Alaska. Ecology 75(6): 1736-1752.
- Thitithanakul, S. (2012). Effect of nitrogen supply before bud break on early development of the young hybrid poplar. PhD thesis. Universite Blaise Pascal, Clermont-Ferrand II.
- Tyree, M. T. and Dixon, M. A. (1986). Water stress induced cavitation and embolism in some woody plants. Physiol Plantarum 66(3): 397-405.
- Urli, M., Porte, A. J., Cochard, H., Guengant, Y., Burlett, R. and Delzon, S. (2013). Xylem embolism threshold for catastrophic hydraulic failure in angiosperm trees. Tree Physiol 33(7): 672-683.
- Zwieniecki, M. A. and Holbrook, N. M. (2000). Bordered pit structure and vessel wall surface properties. Implications for embolism repair. Plant Physiol 123(3): 1015-1020.
Article Information
Copyright
© 2017 The Authors; exclusive licensee Bio-protocol LLC.
How to cite
Readers should cite both the Bio-protocol article and the original research article where this protocol was used:
- Charrier, G., Burlett, R., Gambetta, G. A., Delzon, S., Domec, J. C. and Beaujard, F. (2017). Monitoring Xylem Hydraulic Pressure in Woody Plants. Bio-protocol 7(20): e2580. DOI: 10.21769/BioProtoc.2580.
- Charrier, G., Torres-Ruiz, J. M., Badel, E., Burlett, R., Choat, B., Cochard, H., Delmas, C. E., Domec, J. C., Jansen, S., King, A., Lenoir, N., Martin-StPaul, N., Gambetta, G. A. and Delzon, S. (2016). Evidence for hydraulic vulnerability segmentation and lack of xylem refilling under tension. Plant Physiol 172(3): 1657-1668.
Download Citation in RIS Format
Category
Plant Science > Plant physiology > Abiotic stress